The current state of postharvest, as is often the case, revolves around three food issues — safety, quality, and waste. And then there is the current state of the world.
“All these pressing issues in our pandemic world are accelerating investment in innovations for the postharvest packinghouse,” Ernest “Boomer” Cardinale, U.S. Director of Marketing and Business Development with Decco, says. “The larger food storage and packing facilities are investing in automation, including robotics, to help close the gap in labor disruption. Automating routine functions, like packing, loading, and quality assurance, through AI (Artificial Intelligence) and robotics are game changers but still reserved for the larger well-funded operators. Once economies of scale are met, these automated solutions will be more accessible to all levels of operators.”
Until then, the industry has plenty to discuss on the usual fronts:
FOOD SAFETY
The most pressing postharvest issue, according to iFoodDS, is the ever-evolving microbial testing requirements from regulatory agencies and industry associations.
“Many different commodities from different lots are mingled during processing, which makes precise traceability challenging. Inconsistent lotting definition within the industry makes this more of a challenge,” iFoodDS Director of Customer Success Aaron Schneider says. “The industry is addressing this challenge by establishing process flows that enable accurate tracking and separation of products. This may require advanced tools, like software, tracking labels, and other technology solutions designed for traceability.”
HeavyConnect CEO Patrick Zelaya cites the possibility of a new Food Safety Management Act (FSMA) traceability rule.
“Growers need to get traceability data out of the field and pass it on to partners, including processors and coolers,” he says. “The industry is racing to offer stronger traceability tech platforms, but right now most are not in the hands of growers and can be challenging to implement since they aren’t integrated with other systems that growers are using now for other functions, like food safety and quality compliance.”
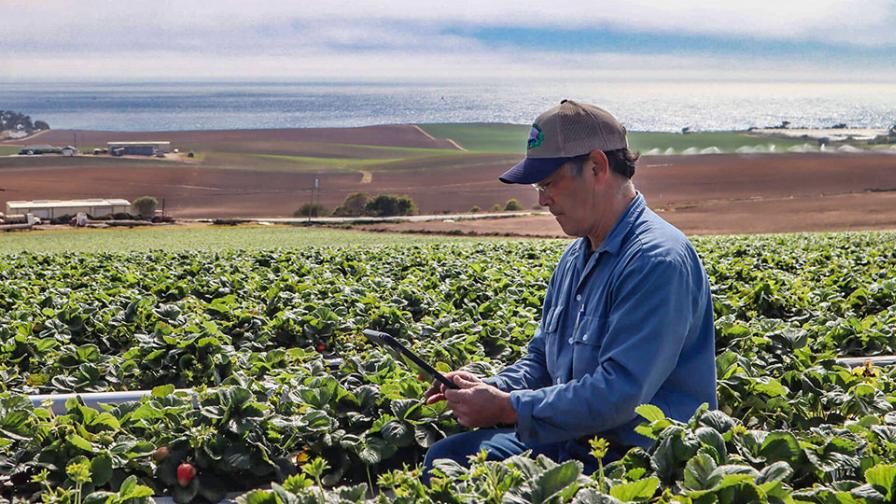
HeavyConnect’s customers include growers, processors, coolers, and shippers who use its app and dashboard to track food safety, worker training, quality control, and supplier management.
Photo courtesy of HeavyConnect
The Global Food Safety Initiative (GFSI) has updated its standards to require 100% food safety audit scores. Unfortunately, there is often limited visibility or data sharing to improve coordination among growers, processors, and packers, according to Provision Analytics Chief Marketing Officer Kevin Davies.
“In documenting seed, spray, and harvest activities for compliance, growers inherently track their product quantity by variety and location. The same is true through wash, cut, pack, storage, and shipping forms,” Davies says. “It’s unnecessary to manually calculate inventory or manually trace process stages.”
FOOD QUALITY
Clarifruit estimates that 25% of the transactions in the industry are impacted by quality mismatches, representing the primary root cause for all inefficiencies in the supply chain, CEO Elad Mardix says. Quality mismatch is a “lose-lose situation,” he says, in which sellers do not get the price they want, and buyers do not get the quality they expect. The solution, he adds, is for the industry to adopt next-gen technologies that digitize the entire quality control (QC) process.
“Given the current limitation of manual QC processes with limited data and analytics, those buyers are struggling with the amount of data surrounding them,” Mardix says, “resulting in significant quality mismatches from both sides — rejections to the growers and rejections from their customers.”
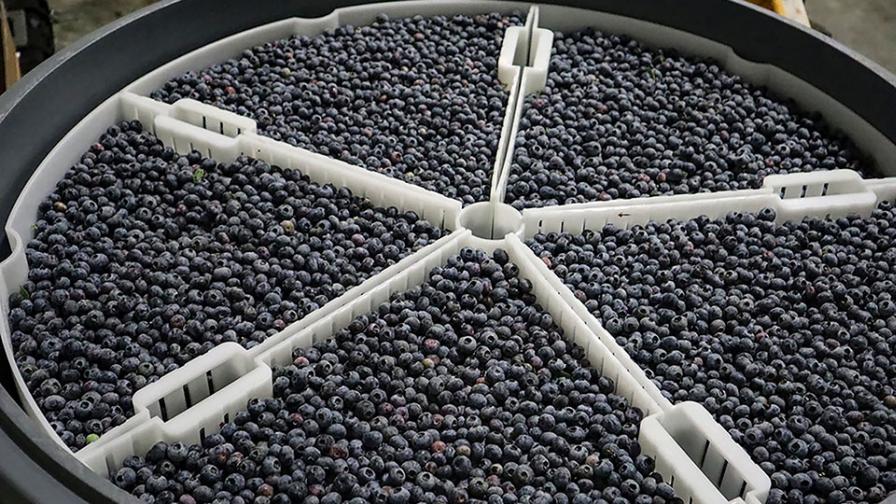
RipeLocker’s container technology moni-tors and changes storage parameters as perishables age. This slows senescence, stops dehydration, and suppresses pathogen growth (decay) on fruit.
Photo courtesy of RipeLocker
FOOD WASTE
The battle remains constant against produce decay, firmness loss and weight loss, and other postharvest issues that can reduce overall product satisfaction, Narciso Vivot, Commercial Director of Business Diversification, AgroFresh, says. “Growers and packers need to find reliable solution providers that are capable of understanding the history of the industry and combine true experience with innovations that can handle whatever challenges may arise, not just one simple solution,” Vivot says.
At RipeLocker, grower partners are seeking improvement in postharvest operational efficiencies to not only reduce defects but also decrease food loss and waste. According to Director of Marketing Selynn Vong, delaying senescence or degradation of fruit to prolong its freshness and tasting quality is attainable through technologically advanced postharvest solutions that do not involve additional coatings, fungicides or picking fruit green before natural ripening. This disruptive innovation in a hi-tech low-atmosphere storage solution allows for the picking of fruit at later stages of the ripening process, resulting in healthier and better tasting fruit, she says.